Making foams, in other words introducing gas to a solid or liquid, is needed in industries like construction, composites, home care and personal care. Solid foam is a clever way to produce lightweight structures and insulation materials, whereas many personal care and detergent formulations are required to form a liquid foam.
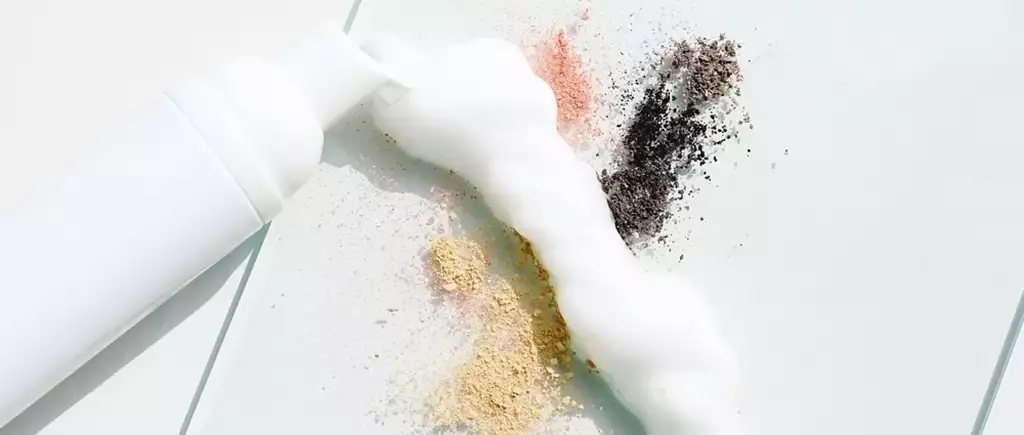
Having trouble producing stable foams?
To produce solid foams, you need a blowing agent which introduces gas bubbles to the solid, and a solid (often a polymer) that hardens around them. Liquid foams are mainly created by use of surfactants and the in of air.
Bubbles to your bath tub
Many personal care products should form a foam when they are used as, for example in bubble bath products and shampoos. The bubbles are needed to make it easier to apply, for example, shampoo to your hair, and because the foam gives an impression of an effective, luxury product. In cleaning products, a stable foam allows a longer contact time with surfaces, thus improving the cleaning outcome.
MFC can help make long-lasting liquid foams as it has a high yield stress, is a good stabiliser, and it is compatible with surfactants. However, MFC does not affect the surface tension and it is not a surfactant, so it should be combined with surfactants to produce nice foams.
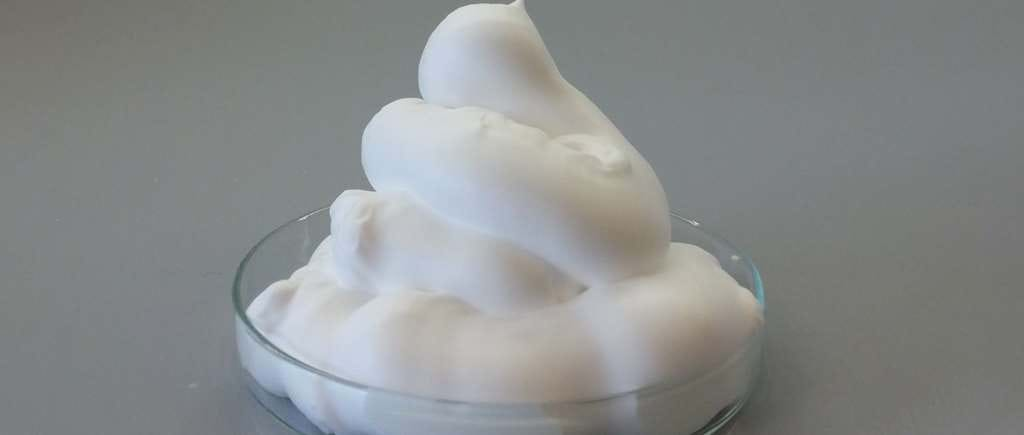
Figure 1. Shaving foam stabilised with MFC (Exilva®, Borregaard).
Insulation structures
Many insulation materials, like expanded polystyrene (EPS), are solid foams. The gas trapped inside the matrix improves the insulation properties dramatically. Lately, there have been attempts to make biodegradable, sustainable solid foams to replace oil-based products. For instance, polyvinyl alcohol (PVOH) and polylactic acid (PLA) can be combined with MFC to create a green foam composite. Zhao et al. compounded MFC in the PVOH matrix and then made foam by extrusion, using super critical CO2 and water as blowing agents. MFC acted as a cell nucleating agent and helped control the cell structure. In Boissard’s et al. work, the water that follows with MFC acted as a foaming agent for PVOH. With MFC, they were able to produce low-density material.
Potentially, MFC could also strengthen foam composites as the fibres are mechanically very strong. Cellucomp has successfully utilised this in their Cellufoam material which could be used to replace EPS in, for instance, helmets.
Foaming is not always desired!
When introducing MFC into a formulation, high shear mixing is needed. If you happen to also have surfactants in the formulation (as is often the case), you experience foaming. MFC is making that worse by stabilising the foam. MFC fibres tend to get into the foam and after a while you have a stable foam on the top, with the MFC and the rest of the formulation is at the bottom. To avoid this, you need either use an airless mixer or add defoamer to your formulation. Where the foaming is desired, MFC can show a sustainable approach to achieving this – whether it is liquid or solid foam.